The procedure of CNC machining entails the usage of a computer system to regulate equipment devices for an extra consistent and dependable outcome. Specialized techniques and tools are commonly used to maximize the machining process, which can include utilizing reducing devices covered with tough materials to reduce wear and enhance efficiency when working with soft metals like copper.
Discover copper cnc machining how copper CNC machining merges advanced technology with sustainable practices to create elaborate, high-precision components, driving development across industries like electronics, automotive, and aerospace.
Amongst the main advantages of CNC machining copper is the capability to generate complicated shapes that traditional machining approaches might not fit. The repeatability of the CNC machining process ensures that mass manufacturing of copper parts keeps harmony, therefore meeting rigorous sector requirements.
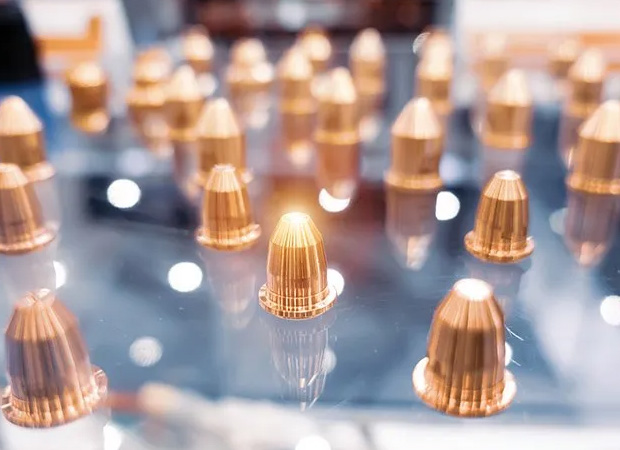
Temperature management plays an essential duty in the CNC machining of copper as a result of its capability to carry out heat swiftly. High-speed machining can cause considerable warmth generation, which might adversely affect the buildings of the copper and worsen tool wear. Consequently, CNC machinists usually transform to sophisticated cooling approaches, such as flood coolant systems and haze lubrication, to take care of warm and extend device life. By controlling the temperature level throughout machining, makers can achieve far better surface finishes, improve accuracy, and generate get rid of boosted mechanical residential properties. Additionally, with the arrival of technologies like high-pressure air conditioning systems and ingenious reducing fluid solutions, CNC machining can accomplish optimum performance while adequately taking care of thermal effects.
The sustainability element of CNC machining copper is not to be forgotten. Copper is a highly recyclable product-- recycling copper needs approximately 90Discover countersink size chart exactly how copper CNC machining combines sophisticated modern technology with sustainable techniques to produce elaborate, high-precision parts, driving development throughout sectors like electronic devices, automotive, and aerospace. much less power than mining and processing new copper ore. CNC machining, paired with sustainable methods, can lower waste by enabling suppliers to utilize scrap copper from various other procedures. The integration of recycling and eco-friendly techniques into machining procedures straightens with the increasingly eco-conscious worths of markets and customers alike. As businesses aim to lower their carbon footprint and enhance their ecological stewardship, CNC machining can play an essential function in assisting in these purposes by supporting recyclable materials flow within the supply chain.
In enhancement to sustainability, cost-effectiveness is one more essential factor for makers picking CNC machining for copper components. The initial financial investment in CNC machinery may be considerable, the long-lasting advantages can surpass the costs. CNC machining offers a reduction in labor expenses because of its computerized nature and diminishes the need for comprehensive hands-on treatment. The specific control & repeatability offered by CNC technology decreases scrap rates, reducing material costs. Additionally, for little to medium set production runs, CNC machining can verify a lot more affordable contrasted to typical machining procedures, as it allows for seamless adjustments and design changes without comprehensive retooling. This capability to pivot swiftly can be useful, particularly in fast-paced industries where market demands can move all of a sudden.
As innovation develops, the functionalities within CNC systems are expanding, better boosting the capacities of copper machining. These simulations allow better preparation of device courses and illuminate how the copper product will certainly respond throughout the machining procedure.
Education and learning and know-how in CNC machining are crucial for recognizing the complete potential of copper procedures. Proficient machinists should be adept in analyzing style specifications, picking the proper tools, and adjusting machining criteria to reduce issues linked with copper's distinct machining characteristics. In addition, the improvement of additive manufacturing modern technologies, such as 3D printing, has actually produced new standards in the processing of copper. Hybrid machining, which incorporates conventional CNC machining methods with additive production, is becoming a viable approach for creating intricate copper parts, blending the strengths of both modern technologies and potentially revolutionizing just how producers approach copper manufacturing.
In the world of research and advancement, CNC machining is assisting the exploration of new copper alloys to improve efficiency even more. As worldwide industries function towards better energy effectiveness, copper's function as a conductor in digital circuits will certainly remain critical, driving demand for sophisticated machining remedies.
The aerospace and auto sectors are additionally eager adopters of copper CNC machining, specifically where light-weight components are of critical importance. As the shift toward electric and hybrid cars continues, the need for high-performance copper parts will likely surge, thus pushing the requirement for sophisticated CNC machining techniques that make certain performance and top quality in manufacturing.
As CNC machining modern technology proceeds to develop, it allows for further automation, where fundamental processes such as device adjustments, examinations, and upkeep can be set right into the manufacturing cycle. This development implies that producers will be able to accomplish greater efficiency levels, shorter preparations, and better versatility in fitting customized requests or variants in layout. Consequently, services that participate in CNC machining operations are better suited to pivot in response to the changes in customer and market needs, promoting growth in an increasingly competitive landscape.
Discover countersink size chart how copper CNC machining combines innovative modern technology with sustainable methods to produce intricate, high-precision parts, driving technology throughout markets like electronics, automotive, and aerospace.
The global industry for CNC machining of copper is experiencing substantial development, influenced by factors such as the surge of clever innovations, electric lorries, and continuous efforts to enhance power effectiveness across numerous applications. It shows a converging trend where organizations accept digital production methods, assisting shape the future of production. Establishing partnerships with distributors, innovation service providers, and academia can boost access to the most recent technologies and understanding within the field, cultivating a collective atmosphere that drives forward-thinking initiatives. In this ability, training and evolution growth stay paramount; buying labor force education on CNC machining techniques, advancements, and material scientific researches will encourage makers to stay in advance of the curve.
As markets advance and the boundaries of technology broaden, welcoming CNC machining's possibility will be essential to understanding extraordinary development and technology in the utilization of copper products. The synergy of copper's material residential properties with innovative CNC machining techniques declares a new age in which effectiveness, sustainability, and precision work together to produce advanced parts that will certainly specify the future of manufacturing and beyond.